There are some advantage and challenges embedded with the production system of Toyota. This paper will analyse the pros and cons of Toyota production system.
Advantages of Toyota Production System
The biggest advantages with Toyota Production System are analysed below.
- Less flaws
- Less wastages
- Less costs
- Less inventory
- Less work-in-process time
- Less employee turnover
- Less production time
- Greater flexibility
- Varieties of products and finally
- Greater and quick responses to the demands of customers
The advantages have been derived from the application of lean manufacturing technology. All the employees of the company are well trained and empowered to make a decision. As a result, any flows in the production system has been revealed very easily and the flaws can be solved soon because the employees are empowered and trained to correct the problem. As a result there is less flaws in the production system.
The overall maintenance system has rooted the way to make less wastage in the production system because the main production philosophy of TPS is to make less wastages by taking care of the production system. As a result there has been less wastages which contributed to farted development of quality product.
The JIT system of Toyota is embedded with the suppliers and the demand side, and all the parties of the system work very closely. Therefore, the company has become successful in making less inventory in its production system. On the other hand the production is initiated from the demand side, therefore, there is less inventory. The suppliers supply products when needed, and the amount that is needed. Therefore, the costs of inventory is minimum in TPS.
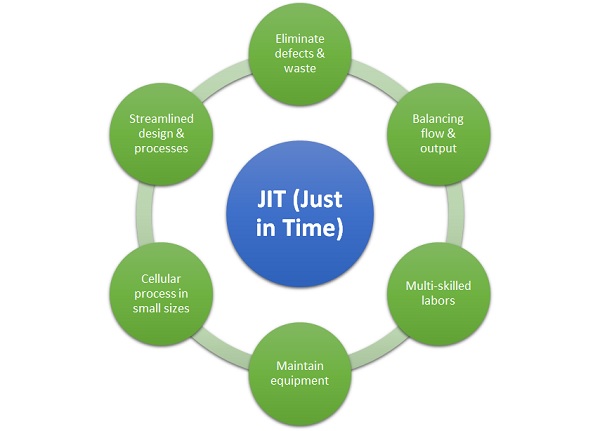
Continuous improvement of TPS has made it possible to make the production system more efficient and the flexibility has helped the company to produce a car within 7 days where competitors can do the same job in 30 days.
As the production system of the Toyota is flexible and it can quickly respond to the market demand, this is very possible to make varieties of products according the demand of the customers.
You might also find below blog posts interesting:
Differences between Toyota and Ford production system
Ford implemented lean manufacturing in Production System
Challenges
One of the biggest challenges of the company is that it is not vertically integrated and thus it needs to depend of the suppliers. On the other hand the competitors such as GM is vertically integrated and thus it can respond more quickly in case of rapid changes of preferences because it can produce its product, on the other hand Toyota needs to depend on suppliers for many parts.
This problem can be avoided by integrating the production system with the suppliers so that suppliers can be informed about the demand in every minutes. Another problem is the TPS implementation time. The company needs to wait years to implement the system in its factories.
On the contrary, the competitors take only 2 years to implement a new system. Toyota should visit the implementation strategies at the competitors to learn how to implement a new system within short time. Thus the company can be swift in TPS implementation.
[…] Pros and cons of Toyota Production System […]
[…] Pros and cons of Toyota Production System […]
[…] Pros and cons of Toyota Production System […]
[…] You might also be interested in: Operations Management of Ford Differences between Toyota and Ford production system Pros and cons of Toyota Production System […]